Time Framework
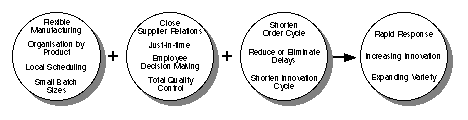
The key differences of time-based competitors appear to be:
- They view the entire system, including suppliers, distributors,
and customers, rather than considering only individual functions.
- They focus on reducing "non-value-adding" time
rather than trying to make people or machines work harder or
faster on value-adding activities.
- They give the measurement of time and responsiveness the
same priority as, if not higher priority than, the measurement
of cost.
As a strategic weapon, time is the equivalent of money, productivity,
quality, even innovation. The ways leading companies manage time
- in production, in new product development and introduction,
in sales and distribution - represent the most powerful new sources
of competitive advantage. Cutting-edge Japanese companies are
capitalising on time as a critical source of competitive advantage:
shortening the planning loop in the product development cycle
and trimming process time in the factory - managing time the
way most companies manage costs, quality or inventory. In the
early 1960s, the Japanese shifted their strategy, using capital
investment to boost work-force productivity. They inaugurated
the era of scale-based strategies, achieving high productivity
and low costs by building the largest and most capital-intensive
facilities that were technologically feasible.
In the mid 1960s top Japanese companies turned to the focused
factory as a new source of competitive advantage.
In the late 1960s leading Japanese manufacturers moved towards
the flexible factory as a new source of competitive advantage.
Two developments drove this move. First, as they expanded and
penetrated more markets, the narrow product lines of their focused
factories began to pinch, limiting their ability to grow. Second,
with growth limited, the economics of the focused factory strategy
presented them with an unattractive choice: either reduce variety
further or accept the higher costs of broader product lines.
The Toyota (flexible factory) system was, according to its
inventor, Taiichi Ohno "born of the need to make many types
of automobile in small quantities with the same manufacturing
process". With its emphasis on just-in-time production,
total quality control, employee decision making on the factory
floor, and close supplier relations, the Toyota system gave the
many Japanese manufacturers who adopted it in the mid-1970s a
distinct competitive advantage. They were enabled to produce
a greater variety of products and introduce new products much
more rapidly.
They managed structural changes that enabled their operations
to execute their processes much faster. As a consequence, time
became their new source of competitive advantage.
While time is a basic business performance variable, management
seldom monitors its consumption explicitly - almost never with
the same precision accorded sales and costs. Yet time is a more
critical competitive yardstick than traditional financial measurements.
Today's new-generation companies compete with flexible manufacturing
and rapid response systems, expanding variety and increasing
innovation. A company that builds its strategy on this cycle
is a more powerful competitor than one with a traditional strategy
based on low wages, scale or focus. These older, cost-based strategies
require managers to do whatever is necessary to drive down costs:
move production to or source from a low-wage country; build new
facilities or consolidate old plants to gain economies of scale;
or focus operations down to the most economic subset of activities.
These tactics reduce costs but at the expense of responsiveness.
In contrast, strategies based on the cycle of flexible manufacturing,
rapid response, expanding variety and increasing innovation are
time based. Factories are close to the customers they serve.
Organisation structures allow fast responses rather than low
costs and control. Companies concentrate on reducing if not eliminating
delays and using their response advantages to attract the most
profitable customers.
In general, time-based manufacturing policies and practices
differ from those of traditional manufacturing along three key
dimensions:
Length of production run
Shorten production runs as much as possible. Reduced run lengths
mean more frequent production of the complete mix of products
and faster response to customers demands.
Organisation of process components
Time based factories are organised by product. To minimise
handling and moving of parts, the manufacturing functions for
a component or a product are as close together as possible. Parts
move from one activity to the next with little or no delay. Because
the production process eliminates the need to pile and re-pile
parts, they flow quickly and efficiently through the factory.
Complexity of scheduling procedures.
In time based factories, local scheduling enables employees
to make more production control decisions on the factory floor,
without the time-consuming loop back to management for approval.
The next challenge is to avoid dissipation of factory performance
improvements in other parts of the organisation, for example
in Sales and Distribution and in Innovation/Product Development.
References
- Stalk, George. Jnr., "Time - The Next Source of Competitive
Advantage". Harvard Business Review, July-August 1988.
- Stalk, George. Jnr., "Time - The Next Source of Competitive
Advantage". Quality Progress, June 1989, pp 61 - 68. (Reprint
of the above)
|